This study, locally known as the ‘Glow and Grow’ project, monitored the growth and development of two aquaponic microgreen crops: mizuna (a Japanese mustard green) and a 7-crop braising mix.
+27% Yield Boost in Microgreens Trial
Case Study from | UbiGro
ABOUT THE PROJECT
This study, locally known as the ‘Glow and Grow’ project, monitored the growth and development of two aquaponic microgreen crops: mizuna (a Japanese mustard green) and a 7-crop braising mix. These crops were grown under an orange-red UbiGro luminescent quantum dot (QD) greenhouse film, and identical crops were grown in a control area without a QD film.
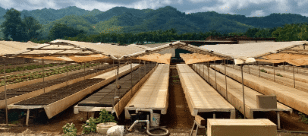
Figure 1. QD film installation at Kunia Country Farms on the island of Oahu, Hawaii.
EXPERIMENT
At Kunia Country Farms in Oahu, Hawaii, UbiGro QD greenhouse films emitting 600 nm were installed above 3,200 ft2 (297 m2) of aquaponic floating raft tabletop grow beds, sheltered with an open-sided polycarbonate greenhouse cover structure. An identical neighboring area in the greenhouse was chosen to serve as the control group, where no QD films were installed. Crops were grown using the farm’s standard aquaponic nutrients.
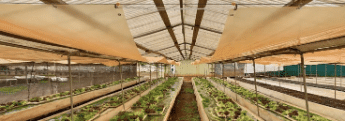
Figure 2. QD films were installed above aquaponic float grow beds in Oahu, Hawaii. Above the film is the polycarbonate greenhouse roof.
Harvest datasets were collected from April through November, covering nine different harvests; over 74 flats of crops were harvested. For wet weights, flats (2’x4′) of mature microgreens from both sides of the experiment were randomly chosen, photographed, cut at the stem, bagged, and weighed, following the farm’s standard harvest procedures. Spectra were recorded during install week to quantify the color-shifting effects of the QD films on the sunlight spectrum.
HARVEST DATA
Plants grown under the QD film exhibited larger wet weights for every mizuna and braising mix harvest. Average wet weights for each harvest are shown in Table 1, and in the form of bar plots is in Figure 3. The average wet weight yield increase was +15.3% for mizuna and +35.8% for braising mix. Taken together, the yield improvement across both crops was +27%.
These micro greens are fast turnaround crops taking just two weeks from seeding to harvest. The yield increases observed here could be converted into faster turnaround if the grower would rather have the exact yield in less time. In this case, mizuna could be harvested ~2 days earlier than if the QD film was not used, and the braising mix could be gathered ~5 days earlier. The harvest results were analyzed with a t-Test (two-sample assuming unequal variances), and corresponding p-values are shown in Table 1.
This analysis showed that the yield improvements observed for both crops were statistically significant beyond a 95% confidence threshold, meaning that the difference was highly likely to be a result of an existing relationship: namely, the spectral change and diffusion of sunlight caused by the QD film.
Table 1. Harvest data for two types of microgreens grown under UbiGro QD films and without (control) across nine different harvests in 2022.
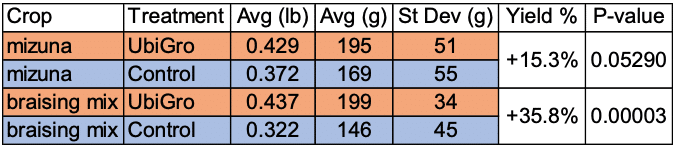
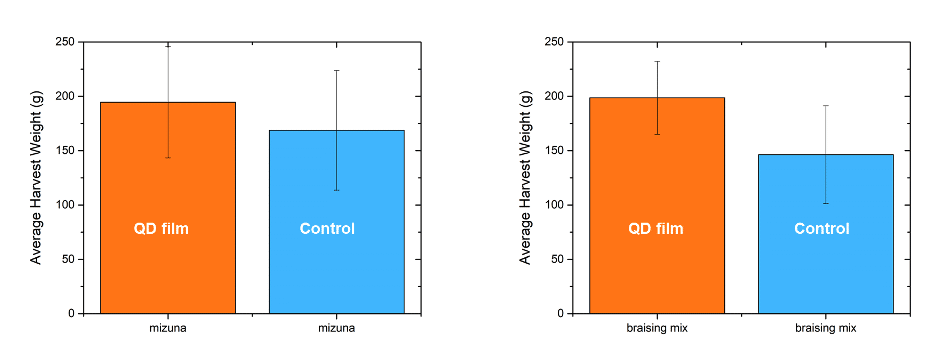
Figure 3. Average wet weight yields for harvested flats of microgreens throughout the experiment.
Photos are shown below that exemplify the yield differences.
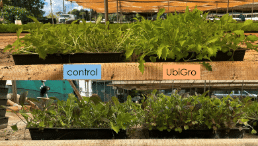
Figure 4. Top: mizuna flats photographed in profile. Bottom: braising mix flats photographed in profile.

Figure 5. Left: mizuna flats photographed from overhead. Right: braising mix flats photographed from overhead.
Economic Impact of Yield Increase
The economic impact of the QD film can be evaluated by comparing the value of the yield increase to the cost and the lifetime of UbiGro. Let’s take a single 4′ x 100′ tabletop grow bed as an example. This 400 ft2 area regularly produces 100 lbs of microgreens each harvest, or 2,600 lbs each year (bi-weekly harvest). The farms sell microgreens at $6/lb wholesale, so the table produces $15,600/year in revenue. A +27% yield boost for the same area would produce an extra $4,212/year/table. Per square foot, that’s an additional +$10.53/ft2/year. The grower estimates a nearly 100% gross margin on the excess production since there is no extra seed or labor cost.
Now we must compare this extra revenue to the cost of the QD film, which is $3/ft2 + shipping and installation, or $4/ft2 as an estimated installed cost. The excess yearly revenue due to the yield increase exceeds the cost of the film. This corresponds to a super fast payback time of just 4.5 months. The QD film has a lifetime of 4+ years in a greenhouse. The QD film will realize profits for the greenhouse over 3.5 years after it has been paid back. UbiGro is an excellent fit for Hawaiian microgreens, increasing greenhouse cultivation’s sustainability and profitability. Many local factors contribute to this: (1) year-round sun, (2) high sun intensity, (3) high produce prices, and (4) high electric costs making lighting impractical.
Seedling Imaging
Another dataset was recorded at Kunia Country Farms to assess the QD film’s impact on seedling germination and growth. After one week, high-resolution overhead photos of mizuna seedling flats were captured randomly from each side of the experiment. Images were processed in Image-J using the Color Threshold tool to quantify the amount of seedling leaf area in each photo. Examples of these photos are shown in Figure 6 below.
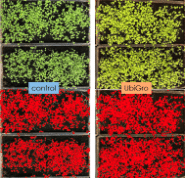
Figure 6. Overhead photos of mizuna seedlings at 1 week maturity. Top row: Raw photos; Bottom row: processed photos in ImageJ, where the red area is calculated as seedling area. Seedling areas from the control and UbiGro sides are compared. In this photoset, the relative difference was +33% more leaf are on the UbiGro side.
Over three different datasets taken from September to November, the aggregate difference in seedling leaf area was +14.4% in favor of the UbiGro side. This evidence suggests that the QD film assists in seedling germination and development, and this benefit is seen at least 1 week prior to harvest.
The content & opinions in this article are the author’s and do not necessarily represent the views of AgriTechTomorrow
Comments (0)
This post does not have any comments. Be the first to leave a comment below.
Featured Product
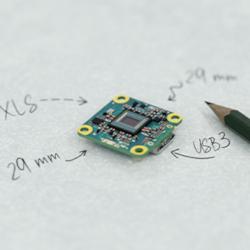