ABB survey reveals unplanned downtime costs $103,000 per hour
According to the new “Value of Reliability” survey from ABB, 69% of industrial businesses experience unplanned outages at least once a month, compared to 69% globally. This costs the typical US business* close to $103,000 per hour, compared to $125,000 globally. Despite this, 22% of US businesses surveyed still rely on run-to-failure maintenance.
The survey, conducted by Sapio Research in July 2023, gathered responses from 3,215 plant maintenance decision-makers globally across the energy generation, plastics and rubber, oil and gas, wind, chemicals, rail, utilities, marine, food and beverage, water and wastewater, and metals sectors. It is part of a report that provides insights into how businesses currently manage maintenance and how they can reduce unplanned downtime.
The findings demonstrate the importance of equipment reliability and maintenance. Globally, 92% reported that maintenance has increased their uptime in the last year, with 38% reporting an improvement of at least a quarter. Also, three-quarters of respondents said that reliability positively impacts their business reputation and financial performance, and helps them meet contractual obligations, prevent waste and secure repeat business. Reliability was rated by respondents as the top priority when purchasing new equipment.
Looking forward, 60% plan to increase their investment in reliability and maintenance in the next three years, with a third planning to boost spending by more than 10%. Nine in ten respondents expressed interest in outcome-based maintenance agreements. Under these, operators pay service partners based on achieved outcomes, such as increased uptime or energy efficiency. This results in efficient and effective service delivery with predictable cash flow.
Speaking about the results of the survey, Rob Snyder, Local Division Manager, Motion Services, said, “Proactive planned maintenance is essential for preventing costly downtime. Without it, organizations are at higher risk for substantive financial losses and the challenge of relying on increasingly difficult-to-source labor. With this in mind, industrial businesses should aim to progress from a high-risk run-to-failure maintenance approach to a long-term outcome-based strategy. This will improve reliability, business reputation, competitivity, cut costs, and provide peace of mind, empowering businesses to focus on their core competence.”
This new, outcome-based model of maintenance will help industrial businesses meet incoming emissions targets and regulations as the world fights against climate change. In addition, it will help overcome the industry skills gap as experienced technicians reach retirement age.
For more information, read the full survey report.
*The survey is based on information provided by third parties in response to a questionnaire, rather than reviewing actual accounting records.
ABB is a technology leader in electrification and automation, enabling a more sustainable and resource-efficient future. The company’s solutions connect engineering know-how and software to optimize how things are manufactured, moved, powered and operated. Building on more than 130 years of excellence, ABB’s 105,000 employees are committed to driving innovations that accelerate industrial transformation. www.abb.com
ABB Motion keeps the world turning – while saving energy every day. We innovate and push the boundaries of technology to enable the low-carbon future for customers, industries and societies. With our digitally enabled drives, motors and services our customers and partners achieve better performance, safety and reliability. We offer a combination of domain expertise and technology to deliver the optimum drive and motor solution for a wide range of applications in all industrial segments. Through our global presence we are always close to serve our customers. Building on more than 130 years of cumulative experience in electric powertrains, we learn and improve every day. go.abb/motion
Comments (0)
This post does not have any comments. Be the first to leave a comment below.
Featured Product
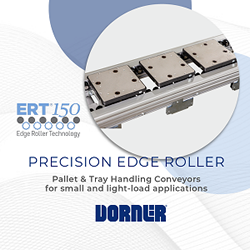