To optimize wear and friction values, shaft and bearing materials that work together harmoniously are crucial. The interdependence of material pairs constitutes a major challenge for bearing and shaft manufacturers.
Maximizing Shaft and Bearing Lifetimes in Agricultural Machinery
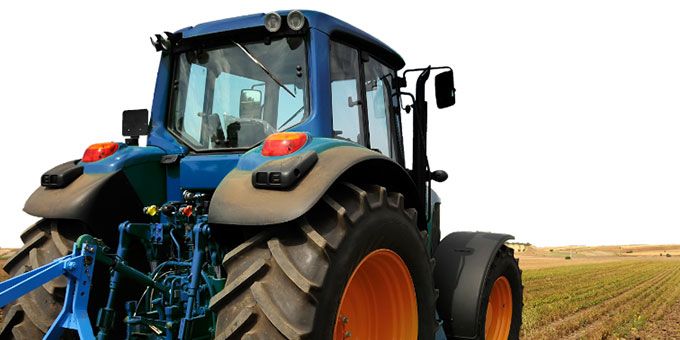
Nick Van Tol | igus
The Problem
One of the most common causes of downtime and failure of agricultural machinery consists of wear on the machinery’s bearings and shafts. Costs incurred by this wear can be high, especially once maintenance and repair costs are factored into lost operation time. According to a 2013 study conducted by the North Rhine-Westphalia Chapter of Agriculture, farmers must take into account the annual cost of repairs, which typically amounts to 2-5% of the purchase price of the machine. In an industry that is constantly evolving technologically, with ever-increasing costs of investments, this creates a huge cost burden for farmers. In order to help trim this massive cost of machine maintenance and repair, machine elements that require no maintenance or lubrication can create large savings, both financially and in terms of downtime.
To optimize wear and friction values, shaft and bearing materials that work together harmoniously are crucial. The interdependence of material pairs constitutes a major challenge for bearing and shaft manufacturers. In terms of shafting, there are various methods of optimizing the shaft material’s surface to maximize performance. Shafts that are too soft tend to wear easily, and can lead to material breakages at high loads. A very rough shaft surface can rapidly wear down the bearing’s surface, and too smooth of a shaft runs the risk of binding or exhibiting the “stick slip phenomenon,” noticeable by a distinctive squeaking. Adhesion increases the coefficient of friction, and therefore, the wear rate of the bearing, though abraded surfaces with a certain roughness offer an effective antidote against this effect.
Because the shaft and bearing form an operational unit, the individual components should always be considered as part of an overall picture. In this sense, the present study will explain the different processes of surface treating shaft materials, and examining the effects on the wear behavior of plain bearings.
To read the white paper click here.
The content & opinions in this article are the author’s and do not necessarily represent the views of AgriTechTomorrow
Comments (0)
This post does not have any comments. Be the first to leave a comment below.
Featured Product
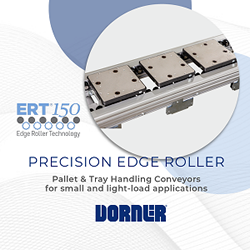