Pipp Horticulture worked with Sozo to implement multi-level Mobile Vertical Racking Systems that allowed them to create 70% more canopy space, totaling 24,824 sq. ft.
Implementing Multi-Level Mobile Vertical Racking Systems
Case Study from | Pipp Horticulture
CASE STUDY
Sozo has a world-class operational facility with 40+ cultivars, leading genetics, and consistently high total cannabinoids and terpenoids. Sozo is committed to using technology, methods, and tools that inspire innovation and maximize sustainability.
ABOUT SOZO
Sozo cultivates, processes (concentrate), and sells quality cannabis products in stores they feel good about. No shortcuts here. They believe plants grown with care produce better outcomes. Whether it’s trichome-encrusted flower or top-quality concentrates, the better the input, the better the output. Each step of their cultivation process comes with a deep sense of care. From the moment seeds are planted, they nurture cultivars to retain full terpene and cannabinoid expression.
PLANNING
Pipp’s team of in-house designers, engineers, and experienced cultivation experts designed a mobile cultivation system that integrated with the other components necessary for successful operation, such as lighting, airflow, irrigation, and drainage systems. All of these tools help Sozo ensure that they are producing the highest quality products possible for their customers.
THE SOLUTION
Pipp Horticulture worked with Sozo to implement multi-level Mobile Vertical Racking Systems that allowed them to create 70% more canopy space, totaling 24,824 sq. ft. in their Detroit cultivation facility. This, along with additional grow solutions such as the ELEVATE™ Platform System, allowed Sozo to greatly improve their workflows and increase their overall output per square footage.
TOOLS FOR SUCCESS
To further improve the efficiency of their grow operation, Sozo added Pipp’s revolutionary ELEVATE™ Platform System, which allows growers to safely access plants on the upper level. They also used products such as ABS Combination Grow Trays and Drying Carts/Racks to allow them to easily access, transport, and care for the plants.
The content & opinions in this article are the author’s and do not necessarily represent the views of AgriTechTomorrow
Comments (0)
This post does not have any comments. Be the first to leave a comment below.
Featured Product
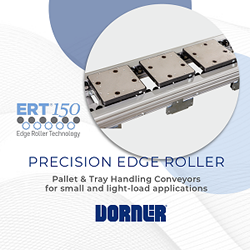