Before using MagGrow, Sparrow could cover an average of 500 acres a day. Now, he can cover 800-1,000 acres in the same amount of time.
MagGrow System helps Fate Sparrow Farm Improve Spray Coverage with Significant Chemical Savings
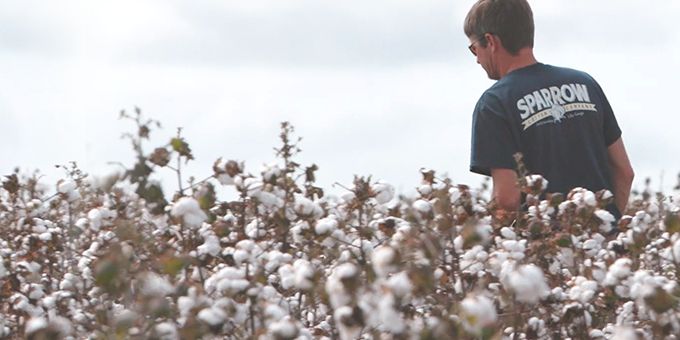
Case Study from | MagGrow
“I’m never going back to spraying more than 5 gallons per acre ever again after my results with MagGrow.”
Fate Sparrow
- Lilly, Georgia
- Cotton
- 3,500 Acres
My Results:
- Reduced Chemical Output by more than 33%
- Increased Acres Covered from 500 to 1,000 per day
- Saved $300k by eliminating a second sprayer
- Significantly Reduced Drift by more than 70%
- Reduced Water Usage
Overview
Third generation cotton farmer Fate Sparrow took over his family’s Middle Georgia cotton and peanut growing operation 18 years ago when he graduated from high school. Over the years, he faced challenges in finding enough labor to run all of his equipment, including two large sprayers. He also struggled with drift issues since he had his sprayer pressure set high. Then he was introduced to MagGrow.
Sparrow admits that he was skeptical at first. He began by putting out his usual 10 gallons of water, dropping it to eight gallons and then eventually to five. He found that using only five gallons worked just as well as putting out 10-15 gallons.
The difference was immediate. “As soon as I turned it on I could tell a 100% difference,” he says.
Before using MagGrow, Sparrow could cover an average of 500 acres a day. Now, he can cover 800-1,000 acres in the same amount of time.
You save 25% of your chemical bill, and that’s huge. That’s the difference in making money and not making money.”
Sparrow was also impressed with the improved coverage he saw with MagGrow. MagGrow converts the liquid chemical into optimal-sized droplets that hit the target, resulting in reduced drift, better coverage and significant chemical savings.
“Before you could see the droplets on the leaves. With the MagGrow system, now it’s like someone painted a sheet of paper across the leaves. You’re getting so much better coverage. You can actually see it under the leaves now. Same nozzles. Same pressure. Same everything.”
His drift problems went away, too. “I’ve had zero complaints about drift this year,” he notes. Sparrow admits that he doesn’t fully understand the science behind the MagGrow system, but he really doesn’t care. He understands how to use it, and he understands the results.
“The MaGrow system is one of the hardest things to understand from a science standpoint, but it’s the easiest thing to use. No electronics, no maintenance. Pop it off that sprayer and throw it on another one and you’re ready to go. At the end of the day you don’t have to clean anything out. It’s just a normal day on the sprayer.”
he importance of delivering the optimal droplet size makes sure the chemical both reaches and adheres to the target.
70% of all conventional spray does not reach the target crop and results in drift and run off, wasting countless dollars.
Why MagGrow?
The MagGrow system helps by creating more of the optimum-sized spray droplets during spraying – the best type that aren’t too big or too small - ensuring that more of the spray goes onto the weeds, crop canopy, buds, flowers, stalk, fruit or vegetable product itself or soil, giving better coverage and more protection.
MagGrow helps improve crop protection, lower risk to the financial investment in the crop, increase the chance of higher crop quality and yield and reduce wastage of expensive resources like chemical inputs, water, time and money.
The content & opinions in this article are the author’s and do not necessarily represent the views of AgriTechTomorrow
Comments (0)
This post does not have any comments. Be the first to leave a comment below.
Featured Product
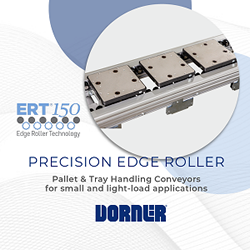