Growing UP: How Conveyor Systems from Ultimation Industries Can Improve Vertical Farming Productivity
Solutions range from simple to sophisticated
Indoor farming is all about maximizing food production per acre, but growers who want to further increase yields should consider growing "up" with the help of conveyor technologies that make use of the available vertical space within a facility, according to Ultimation Industries. Ultimation is the leading direct-to-consumer conveyor manufacturer for the food processing, vertical farming, warehousing, delivery and other industries.
Indoor vertical farming is expected to grow to $9.7 billion worldwide by 2026 from $3.1 billion in 2021, due to higher yields when compared to conventional farming, its capacity for year-round crop production and advances in lighting and other technologies.
"Conveyors are one of the simplest and quickest productivity improvements a fast-growing business can implement and are especially suited to the vertical farming industry," said Richard Canny, president of Ultimation. "Simple roller conveyors or overhead I-beam trolleys can have a payback of days or weeks, while larger custom-built systems often have payback periods of only 3-6 months." Ultimation is currently building the material handling system for what is believed to be the world's largest indoor vertical farming facility.
Perhaps the most obvious way conveyor technologies can help increase indoor farming productivity is by taking advantage of unused vertical space above a work area. Overhead conveyors can lift growing trays when they're not being actively managed and bring them back to operator level for tending and harvesting, allowing more produce to be grown within the same footprint.
Conveyors can also help reduce the manual labor of carrying items by hand, quickly and safely transporting plants from point A to point B. According to Canny, systems can be engineered to seamlessly integrate with harvesting and packing equipment available through Ultimation's expansive partner network.
Ultimation uses materials made of galvanized steel, zinc-plated materials and powder-coated frames which are approved for food-grade applications and are easily cleaned—another productivity savings for indoor farmers. Ultimation can also design systems for hanging towers and growth pods made of food-grade plastic when required.
Different types of conveyor systems are typically used for different parts of the growing process, according to Canny. For example, the sections of the farms where plants are sitting still can use simple, standardized material handling systems. Vertical format conveyors such as hanging towers or horizontal formats such as growing trays can be customized to match the grower's needs.
Once plants are grown, more sophisticated technologies like automated motorized conveyors and automatic storage and retrieval systems are needed to safely move produce to the harvesting area. The most commonly used industrial automation equipment for indoor farming are gravity roller, belt, and skate wheel or flow rail conveyors. These systems use the force of gravity to move the load, allowing the product to roll along the upper surface.
More recently, the technology used in larger vertical farming systems is including motorized and overhead conveyors that take advantage of the generally unused vertical space above the working area. Using curved sections or even lifters, they bring produce down to operator level and back up to higher elevations as needed.
Power and Free conveyors are the ultimate in space and volume optimization for vertical farming systems as they enable tight concentration of product in some areas while also enabling separation of the products for movement to processing areas.
"The best planned and best-run indoor farming facilities take into account the product's growth cycle and will likely use a combination of a conveyor system designs to maximize productivity," said Canny. "Our engineers understand the economics of indoor farming and can help growers design, build and implement material handling solutions that meet their needs and budget."
For more information about using conveyors to maximize indoor farming productivity, visit https://www.ultimationinc.com/.
About Ultimation:
Ultimation Industries, LLC is the leading direct-to-consumer conveyor manufacturer serving the automotive, food processing, vertical farming, heavy equipment, warehousing, fulfillment and delivery industries. The company offers a line of proprietary automation systems and is also the largest integrator of Jervis Webb Conveyor Systems. Ultimation's e-commerce channel sells Ultimation, Interroll, Itoh Denki, Jervis Webb, and a wide range of other conveyor equipment. Ultimation was named a 2022 Michigan 50 Companies to Watch by Michigan Celebrates Small Business. In 2020, Ultimation was recognized as one of Inc. 5000's fastest growing private companies in America. Visit https://www.ultimationinc.com/ for the latest product information and news about Ultimation.
Featured Product
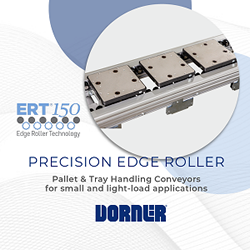
The ERT150 - Dorner's Next Evolution of Edge Roller Technology Conveyors
The next evolution in Dorner's Edge Roller Technology conveyor platform, the ERT®150, is ideal for small and light-load assembly automation, as well as medical and medical-device assembly application. The ERT platform is the only pallet conveyor of its kind available with an ISO Standard Class 4 rating for cleanroom applications. Earning the ISO Standard 14644-1 Class 4 rating means Dorner's ERT150 will conform and not contribute to the contamination of cleanrooms to those standards. As implied by its name, the ERT150 (Edge Roller Technology) uses rollers to move pallets through the conveyor smoothly with no friction (a byproduct often seen in belt-driven platforms). The conveyor's open design eliminates concerns of small parts or screws dropping into rollers and causing conveyor damage or jamming. The ERT150 is suited to operate in cleanroom environments requiring a pallet handling conveyor. It is capable of zoning for no or low-back pressure accumulation and is ideal for automation assembly applications within industries including medical devices, electronics, consumer goods among others.