The purpose of this paper is to help a reader understand what technology can be used to improve profits, the cost to implement such a solution and the estimated payback period based on cannabis prices and labor costs.
Calculating Break Even and ROI When Investing in Sensors for the Cannabis Market
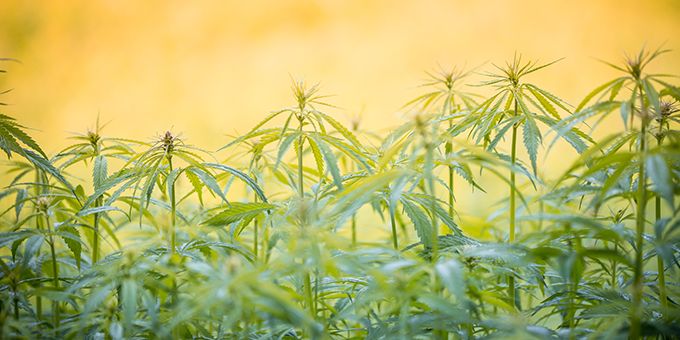
Matthew Nemeth Managing Director | E+E Elektronik
Cannabis is a rapidly growing industry in the United States. As more states legalize the cultivation and sale of cannabis the supply will increase in the market. This increase will push down prices making it increasingly difficult for a grower to make a profit. In order to improve profitability a grower must significantly reduce labor inputs and increase cannabis flower outputs. The key to achieving this is through the integration of sensors and climate technologies to better control growing conditions.
Upgrading to an automated system is expensive but the payback can be quick. The purpose of this paper is to help a reader understand what technology can be used to improve profits, the cost to implement such a solution and the estimated payback period based on cannabis prices and labor costs. Data in this paper was gathered in the same way a manager at a cannabis grower might research – using Google.
SIMULATION DESIGN
Indoor growers use commercial-grade heating and cooling systems and do not rely on regional weather patterns. This setup mimics ideal growing conditions year-round. This allows for multiple grow cycles each year within the confines of the building to maximize revenues.
Room sizes vary. Plant sizes vary. As a result, the variables in real-world applications will be wide. Setting up this simulation involves deciding which size room to create, how many plants can reasonably fit into that space, and what efforts are required to maintain the climate in that area.
In this case a single grow facility is setup. Within each of the 4 grow rooms there is enough space and equipment to grow 100 plants at a time and is derived through the following:
-
A 20 foot by 20 foot growing space is 400 square feet
-
Standard 5-gallon pots are used to grow a cannabis plant
-
Each pot has a maximum diameter of 12 inches (1 foot)
-
Growth outside the pot circumference is estimated at 6 inches (0.5 feet)
-
Based on this, each plant will require an estimated 4 square feet of space
-
400 square feet available in the room divided over 4 square feet required per plant results in 100 plants in the room
For the remainder of this white paper, this setup of these rooms and 100 cannabis plants per room will be used to calculate revenues and costs. All calculations will be shown in full and utilize publicly available information with citations.
ENVIRONMENTAL AUTOMATION AND CONTROL OVERVIEW
Like all plants, cannabis responds positively when in ideal conditions by producing more flower. These flowers are the centerpiece of the plant as they turned into the saleable product. These products include cigarettes, extract, edibles and more. The goal of any grower is to maximize the amount of flowers produced by each plant.
Greenhouses and indoor rooms create an ideal environment for the plant. Artificial lighting is used to simulate sunlight. Heating, ventilation and air conditioning (HVAC) systems are used to control the temperature, relative humidity and air circulation within each room. Mastery of these elements can improve the overall yield of the plant.
A thermostat on an HVAC system is a sensor. When a room gets too cold, the thermostat will automatically turn on the heater and circulate the warm air into the room. When the air gets too dry a humidifier is activated. This is suitable for a home or office but an indoor grow room needs better control.
Improving this control requires the purchase, installation and integration of advanced sensors into the HVAC system. A proper setup will create a room that is automatically monitored and adjusted to maintain the ideal environment for plant growth.
MANUAL PROCESS CONTROL
Manual labor is a big part of operational costs. For an indoor grower monitoring room climate this means a person using handheld devices to measure temperature, relative humidity, carbon dioxide and air flow. These readings are used to make adjustments to the HVAC system.
The process is straightforward; however, the number of data points needed and frequency of measurements makes this a dedicated task. Taking readings at 25 square foot segments of growing space requires 16 measurements per room.
If taking and documenting the reading takes just under 2 minutes then about 30 minutes are needed per room. To manage 4 equally-sized rooms a person will rotate back to the same room every 2 hours. This must be performed every day around the clock.
The complexity of this measurement schedule can simplified visually at this facility:
Figure 1 - Manual Schedule Example to Collect Sufficient Data in Grow Rooms
Manually collecting these points is not cheap. According to the Bureau of Labor Statistics, hourly labor rates for nondurable goods manufacturing is $27.41. A business looking to reduce costs while collecting measurements 24 hours per day will need to employ 3 people to prevent overtime. Based on these numbers, the labor costs associated with collecting data for the facility is calculated as:
$27.41 per hour × 24 hours per day |
= |
$657.84 per day |
$657.84 per day × 365 days per year |
= |
$240,112 per year |
The labor used to collect these could be used for other profit-making tasks. These costs are the focus for improvement using a fully automated system.
AUTOMATED CONTROL SYSTEMS
Data collection, processing and adjustment are tasks that can be performed affordably and reliably with automation. Sensors can take reliable measurements more often and a central control system can make adjustments with better speed and precision than a human.
E+E Elektronik is an Austrian manufacturer of high quality environmental sensors. These can measure temperature, relative humidity, carbon dioxide concentration and air velocity. Placing these sensors in strategic locations around a grow room enables the grower to:
-
Monitor real-time conditions
-
Spot developing microclimates
-
Automatically adjust the conditions
-
Improve circulation in specific areas
For the grow rooms in this facility, taking measurements from 16 locations within each room and monitoring air velocity will replace the manual labor. The list of sensors includes:
Sensor |
Measurements |
Quantity |
Unit Price |
Extended Price |
EE872 |
CO2, RH, Temp |
64 |
$900 |
$57,600 |
EE75 |
Air Velocity |
12 |
$1,100 |
$13,200 |
Sub Total: |
$70,800 |
Installation labor costs will vary by region and complexity of the facility. A controls or electrical engineer is needed to setup the system. In 2020 the median pay of an electrical engineer is $49.71 per hour. For the purposes of this exercise it is estimated that each sensor will take 5 hours to install and test. This will result in 380 hours of engineering efforts, equal to $18,890 in labor. An estimated overhead of 20% is added, bringing the labor total to $22,670.
A controller is needed to receive the inputs from the sensors and make automatic adjustments. Controller sizes can vary significantly. One of the top control manufacturers in North America estimates system costs as low as $10,000 but can range up to $1 million. For this case, a single system to control all 4 rooms is considered. This system is estimated to cost $75,000.
Full integration of the sensors into the controller results in the following capital costs:
Line Item |
Estimated Cost |
Sensors |
$70,800 |
Controller |
$75,000 |
Installation |
$22,670 |
Grand Total: |
$168,470 |
This investment will replace the existing labor expenses and will not be incurred again.
BREAKEVEN BASED ON LABOR SAVINGS
Making the decision to move to an automated process is not easy. The capital investment of $168,470 is required up front. Manual labor is paid as incurred so the expense, while larger, does not consume significant capital immediately.
Before spending any money, a manager will want to know when the cost of the investment becomes equal to the existing manual process. Calculating this is relatively straight forward. Comparing the cost of the investment to the manual process, simply divide the two values:
$168,470 investment ÷ $240,112 labor per year |
= |
0.70 years |
0.70 years × 12 months per year |
= |
8.42 months |
Manual labor cost over 5 years: |
$240,112 × 5 |
= |
$1,200,560 |
Total labor savings over 5 years: |
$1,200,560 - $168,470 |
= |
$1,032,090 |
Return on investment (ROI): |
$1,032,090 ÷ $168,470 |
= |
613% |
Once the breakeven point is reached, the return on the investment is significant. This only highlights the savings resulting from removing manual labor from the process.
ADDITIONAL POTENTIAL GAINS
Automating climate control can increase how much flower each plant produces. The cannabis industry centers on the flower so maximizing its growth maximizes revenues. Price differences for the flower compared to other parts of the plant can be significant:
Figure 4 – Reconstructed Comparison of Cannabis Products
Prices vary by state. The District of Columbia is the highest at $5,500 per pound, which is more than double Nevada at $2,100. Cannabis Benchmarks is an online resource which publishes weekly spot prices for flower by the type of system used to grow the plant:
Cannabis Benchmarks ® US Spot Weighted Average |
|||
|
This Week |
Last Week |
Week on Week Δ |
Total |
$1,384 |
$1,410 |
-1.8% |
Indoor |
$1,779 |
$1,804 |
-1.4% |
Greenhouse |
$1,063 |
$1,113 |
-4.5% |
Outdoor |
$634 |
$642 |
-1.3% |
Copyright © 2021 New Leaf Data Services, LLC. All rights reserved. |
For the week ending on October 29, 2021 the price of indoor cannabis flower is $1,779 per pound. This helps calculate potential additional gains using automation technology. Some aspects to consider include:
-
Published reports indicate achieving 5 cycles per grow room but system installation time in the first year will cap this at 3 cycles
-
Subsequent years will see 4 cycles per grow room
-
As established earlier, this room will contain 100 plants
-
Each plant will produce 1 pound of saleable marijuana flower
Based on spot prices each cycle will generate $711,600. The first year will have 3 growth cycles and generate $2,134,800. Each subsequent year will generate $2,846,400 for a total of $13,520,400 over the 5-year period.
Precisely controlled climate using automation can improve how much flower a plant will produce. This could result in the following additional revenues based on increased yield:
Yield Improvement |
Additional Revenues Year 1 |
Additional Revenues After Year 1 |
1.0% |
$21,348 |
$28,464 |
2.5% |
$53,370 |
$71,160 |
5.0% |
$106,740 |
$142,320 |
Factoring in these additional revenues improves the breakeven and return on investment:
Yield Improvement |
Net Investment |
Break Even |
ROI |
1.0% |
$147,122 |
10 months |
693% |
2.5% |
$115,100 |
8 months |
813% |
5.0% |
$61,730 |
6 months |
1,014% |
These numbers are based on the current spot price of cannabis flower. Regions with a higher price will see these numbers further improve. Regardless of the region, these numbers make it clear that automation is a smart investment.
CONCLUSION
When automation technology is properly integrated into a cannabis grow room, labor can be significantly reduced and overall yield increased. This will result in real monetary returns.
As consolidation in the cannabis industry continues, investors will start to look for ways to maximize their return. An improvement of a few pounds of marijuana per grow cycle may not seem like a lot but the additional revenues quickly add up. This is accomplished by using technology that is affordable, reliable and readily available.
The purpose of this paper is to help a grower think about how technology can be utilized to improve a company’s profitability. The overall benefits of automation technology are immense. Justifying the large up-front investment can be difficult but with a short breakeven and high return it becomes clear that it is the right move for any cannabis grower.
The content & opinions in this article are the author’s and do not necessarily represent the views of AgriTechTomorrow
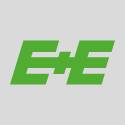
E+E Elektronik
Lowering of energy costs, acceleration of growth and extension of the possible storekeeping duration can be optimised by the precise measurement of humidity, CO2-content and temperature. Optimum basic conditions for animals and plants ensure best agricultural products. As different applications demand various adopted solutions for optimization of agricultural processes, E+E Elektronik provides a broad portfolio of agricultural monitoring products
Other Articles
Ripening Fruit in Ripening Chambers – How Bananas & the Like Ripen in the Best Possible Way
"Growth Turbo" CO2 - How Does CO2 Fertilisation Work in the Greenhouse?
Cosy Climate in the Greenhouse - Climate Sensors Ensure Optimum Growing Conditions
More about E+E Elektronik
Comments (0)
This post does not have any comments. Be the first to leave a comment below.
Featured Product
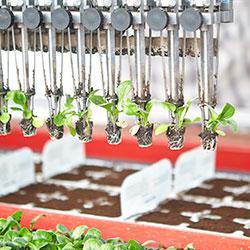